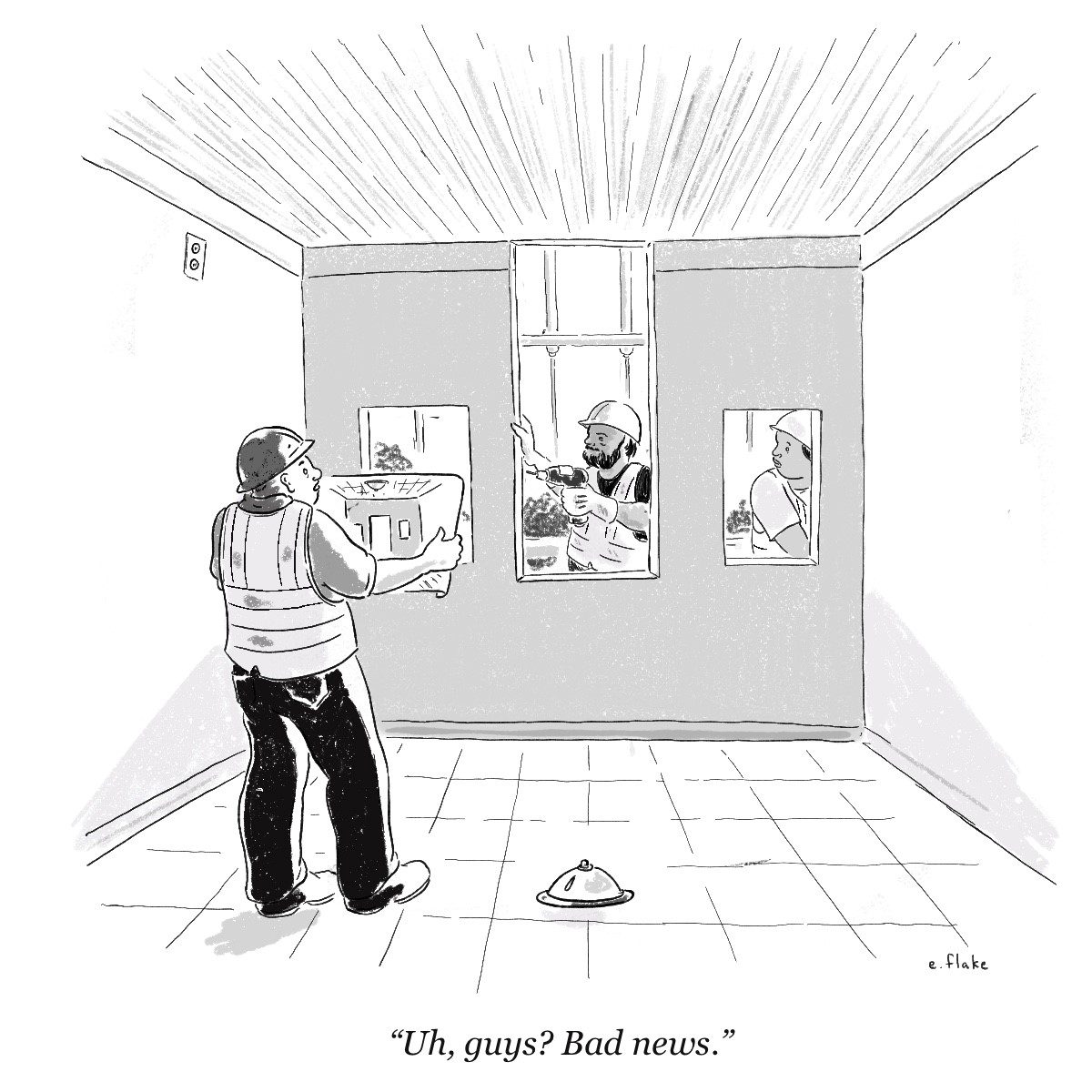
Specify and procure FF&E and OS&E at scale with Fohlio today. Empower teams to move faster and improve their operational workflow with specification, prototyping, procurement, collaboration, and analytics tools.
Let’s play a game.
What’s more expensive than custom marble countertops?
Fixing them after they were incorrectly specified.
Spec errors don’t just cause “a little confusion.”
They cause delays, blown budgets, angry clients, and rework that eats your margins alive.
Even the smallest mistake — a missing finish code, an outdated vendor link, the wrong product dimensions — can trigger a costly domino effect. And once it starts? You’re not just paying for the error. You’re paying for the time, labor, shipping, and stress it takes to fix it.
Here’s what spec errors really cost — in the real world. And how better spec management and specification management can prevent them.
The Cost of Materials — Twice
One typo, and the wrong tile is ordered. Now you’re not just paying for the right material — you’re eating the cost of the wrong one, too.
Example: $35,000 in lighting fixtures scrapped because they didn’t meet code compliance. Oops. The fixtures were gorgeous. They just weren’t UL-rated for the jurisdiction. No returns allowed.
In high-volume rollouts or multi-location builds, even a minor mislabel can mean duplicating an entire order. Effective specification management could’ve caught it.
Rush Fees + Expedited Shipping
Spec errors create last-minute chaos. That means:
- Overnight freight
- Overtime labor
- Vendors who suddenly charge a premium to “help you out”
One missed detail in a vendor spec? That’s a $6,000 FedEx bill waiting to happen.
And that’s not counting the cost of rerouting on-site labor to accommodate the delay. That’s two crises for the price of one. This is where streamlined spec management pays for itself.
Project Delays
The install team shows up. The product doesn’t.
Now you’re rescheduling trades, pushing timelines, and possibly paying liquidated damages.
One project manager shared that a single incorrect furniture spec delayed a hotel opening by three weeks. Multiply that by daily lost revenue across 100 rooms? That’s a six-figure mistake.
Time is money. Spec errors rob you of both.
Read: Safeguard Your Profits: The Cost of Delayed Openings and Ways To Mitigate It
Team Morale and Client Trust
Every time you go back to the client with “Actually, we need to reapprove this…” you lose credibility.
And internally? Your team is exhausted from solving problems they didn’t create.
Designers get blamed for specs they didn’t update. Procurement teams scramble to find compliant replacements. PMs mediate yet another back-and-forth.
You’re not just spending money — you’re spending trust.
Reputation
Spec errors have a long tail. They don’t just affect this project.
They follow you into the next RFP. The next brand rollout. The next pitch to leadership.
Especially if they happen on a flagship or high-visibility project, spec errors can damage future business opportunities. People remember who delivered on time — and who didn’t.
Read: OS&E and FF&E Cost Estimation and Prototyping for Multi-Location Brands: An In-Depth Guide
The Most Common Types of Spec Errors
Let’s get specific. The most common (and costly) spec errors tend to fall into these buckets:
- Incorrect product codes – One digit off, and you’ve ordered a matte black faucet instead of brushed nickel.
- Outdated vendor links – Product pages change or disappear. Specs don’t.
- Discontinued or obsolete products – Especially painful in multi-phase rollouts.
- Wrong finish or material – A chair in the wrong color might seem minor — until it clashes with the brand palette.
- Dimensional errors – 24 inches vs. 42 inches? That’s not a small oversight.
- Mismatched spec versions – Multiple teams, multiple files, no clear source of truth.
Any one of these can derail your project. Combined? It’s a mess. Smart specification management helps prevent every one.
Where in the Workflow Errors Sneak In
Spec errors usually creep in at these points:
- Design handoff to procurement – The designer's intent doesn’t always match what gets ordered.
- During value engineering – Items are swapped for cost savings, but not re-approved.
- During last-minute substitutions – Often done under pressure, without documentation.
- Manual data entry – Especially into Excel or PO systems.
- Lack of version control – Specs float between teams with no audit trail.
Knowing where these cracks exist is the first step to fixing them with better spec management workflows.
Read: 5 Ways to Avoid Budget Creep in Design and Construction Projects With Better Data Management
How Much Are Spec Errors Really Costing You?
A $2,500 error may not sound like much. But across 30 projects a year?
That’s $75,000 in waste — before you even account for lost time, morale, or opportunity cost.
And let’s be honest: Some of these errors cost way more than $2,500.
Manual vs. Standardized Spec Management: A Quick Comparison
Manual Workflow | Fohlio Workflow | |
---|---|---|
Spec Versions | Tracked in spreadsheets | Automatically versioned |
Approvals | Email chains | Logged & timestamped |
Vendor Management | Siloed or memory-based | Centralized + searchable |
Communication | Disjointed | In-platform + visual |
Risk of Error | High | Low |
The choice is clear. Standardization isn’t a luxury — it’s protection.
And it starts with great specification management tools.
How to Catch Spec Errors Before They Become Expensive
Here’s your mini checklist:
- Are all products linked to current, approved vendors?
- Have alternates been pre-vetted and approved?
- Has the client signed off on the final version?
- Is this version of the spec the most recent?
- Is the product code complete, correct, and verified?
The Fix? Standardization + Visibility
Spec errors thrive in chaos: scattered spreadsheets, out-of-date PDFs, buried email threads.
What you need is control:
- Centralized spec templates
- Approval logs with timestamps
- Vendor libraries with verified, compliant products
- Visual tools to avoid miscommunication
- Real-time collaboration across design, procurement, and PM teams
All of which Fohlio handles, by the way.
Because fixing a mistake costs way more than avoiding it in the first place. And that’s the power of smart, scalable specification management.
Want to see how Fohlio helps teams reduce errors, streamline approvals, and protect their margins?
Let’s talk. Book a demo with us here.
Specify and procure FF&E and OS&E at scale with Fohlio today. Empower teams to move faster and improve their operational workflow with specification, prototyping, procurement, collaboration, and analytics tools.
Expore Fohlio
Learn how to:
- Save days of work with faster specification
- Create firm-wide design standards
- Automate and centralize procurement
- Keep your whole team on the same Page
- Manage product data
- Track budget against cost in real time.
- Prepare for asset valuation
Published Mar 28, 2025